Fulfilment Masterclass for High-Value Home and Kitchen Business
FULFILMENT AGAINST A TICKING CLOCK
Introduction
A beloved family-run business, it has illuminated celebrations across the UK for the past two decades. With a stellar reputation and over 5,000 glowing reviews, the company has consistently prioritised customer satisfaction. Their dedication to exceptional service has solidified their position as a trusted name in the industry.
As it sought to expand its reach into the European market, a series of challenges emerged, threatening to derail its ambitious plans. These hurdles included logistical complexities that required careful consideration and strategic planning, which Prolog implemented well.
Prolog really came through for us when our shipment got rejected in Germany. They quickly switched out over 10,000 labels and got everything sorted just in time for the holidays. Super efficient and a huge relief for our EU expansion!
A****, Supply Chain and Logistics Manager
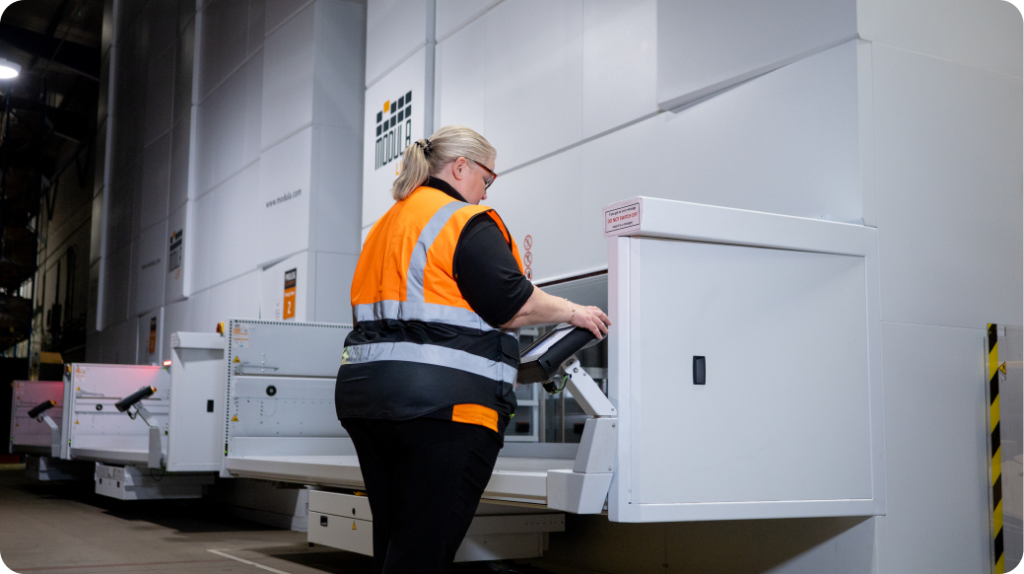
Challenges
While seemingly minor, this oversight triggered a serious breach of EU regulations. EU directives mandate specific safety standards to ensure consumer protection and market integrity. By affixing UK labels, they inadvertently violated these regulations, rendering their products non-compliant within the European Union.
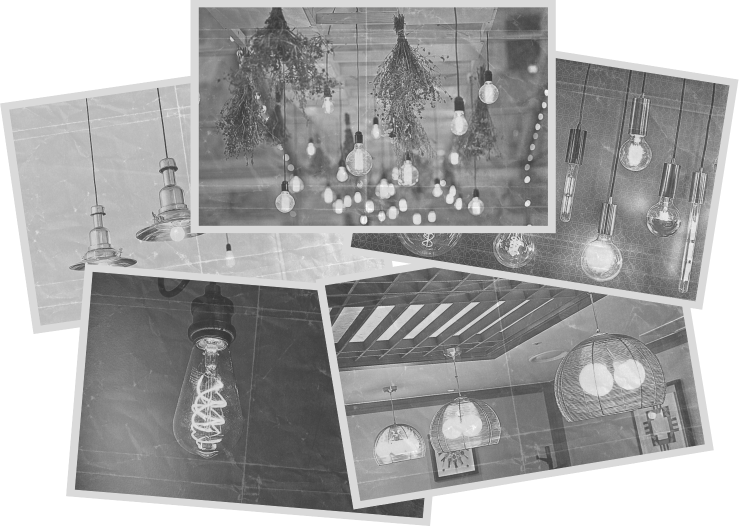
The Remedy
Faced with this critical challenge, the client swiftly wanted us to implement a comprehensive recovery plan. Prolog embarked on an uphill and time-sensitive task involving the following steps:
Goods Retrieving: The rejected containers were called back to our warehouse where our team was ready to unfold their expertise.
Product Dismantling and Inspection: Each product within the rejected containers was meticulously dismantled, removing it from its original packaging.
Label Replacement: Over 10,000 individual labels were applied to cables and plugs, ensuring compliance with EU safety standards. This painstaking process required precision and efficiency.
Repackaging and Palletisation: Once the products were relabeled, they were carefully repackaged to maintain their integrity. Subsequently, the repackaged items were meticulously stacked onto pallets, replicating the original configuration.
Customs Representation: Now that the products are compliant with EU regulations, we prepared the shipment that was processed to meet the custom requirements for Germany. We worked closely with customs authorities to provide the necessary documentation and evidence of compliance.
This innovative and calculated effort, undertaken against the clock, enabled them to navigate the compliance crisis successfully. Prolog’s dedication to quality, attention to detail, and ability to adapt to unforeseen challenges proved instrumental in salvaging the shipment and securing its entry into the European market.
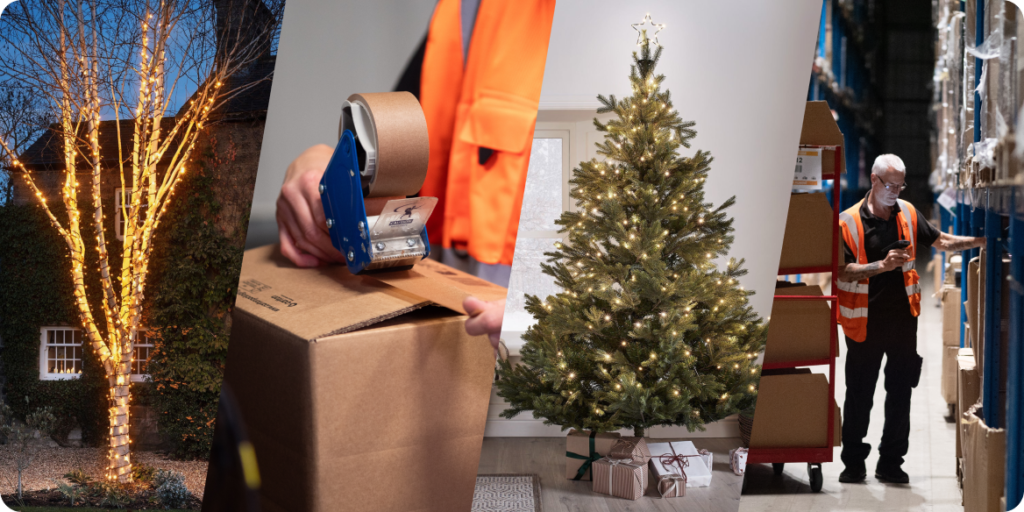
The Outcome
With the help of Prolog’s diligent efforts and the efficient execution of the recovery plan, the shipment of Christmas products was successfully cleared by German customs. This timely intervention ensured the products arrived in the European market for the peak holiday season.
By overcoming the initial compliance hurdle and implementing a swift and effective solution, we demonstrate our commitment to customer satisfaction and ability to navigate complex supply chain challenges. This experience serves as a valuable lesson, highlighting the importance of rigorous adherence to international regulations and the need for robust contingency plans.
Key Takeaways
Problem
The container loads from one of our clients were refused entry to Germany as a Supplier because they had applied UK safety labels to their products rather than EU labels. The customer had 48 hours to move the containers from the Port of Entry to avoid significant charges and penalties.
Solution
Prolog implemented a plan to open every product, remove it from packaging, apply over 10,000 replacement labels to cables and plugs, repackage, re-stack onto pallets and ultimately load (in the same configuration as received) for representation back to German customs. Based on this, the product was accepted by German customs and released to the onward warehouse.